In the world of infrastructure inspection, as we’ve written about recently regarding bridges and dams, drones can improve both operational efficiency and safety for workers. Those workflows are not the only kind of infrastructure inspection, though, and there are some areas which are particularly dangerous, or simply just gross, to the point where people really can’t be down there. That’s where autonomy comes into play. With the ability to autonomously fly a drone through a space, such as a wastewater pipe or a mine, not only is it significantly safer than doing a human-led inspection but it also opens up the possibility to inspect spaces that had previously been inaccessible.
There are a few companies working in this autonomous drone space, one that is certain to expand in the coming years. The U.S.-based Exyn Technologies and Australian-based Emesent are two of the bigger names, and in Europe, Hovering Solutions – based in Spain but operating worldwide – is carving out their place in the industry by offering a full end-to-end inspection workflow centered around autonomous drones.
Fran Espada, Hovering Solutions’ CEO, founded the company in 2016 after working as an electronics engineer and spending a dozen years focused on novel technologies for underground areas. At that job, he discovered a need to inspect those risky underground areas, but also noted a lack of technology to enable the inspections. He then sought out to develop a UAV which could be used for these inspections, resulting in Hovering Solutions’ founding.
Espada recently spoke with Geo Week News about the company, autonomous inspections, and what’s coming down the road.
Providing end-to-end services
Perhaps the thing which stands out the most about Hovering Solutions is how much control they take over entire inspection workflows, separating themselves from some of their competition. Hovering Solutions, as Espada relays, manufactures their drones, has their team members fly the site, and does the data processing in-house to provide both panoramic images – Espada compares this view to what one sees within Google Street View – and 3D point clouds, producing the former within an hour of the start of the flight for a full project. In the web-based visualization tool, all images and 3D point clouds are georeferenced in absolute coordinates, and customers can make measurements of things like cracks and other areas of interest. Moreover, these data sets can be directly downloaded from the web tool in standard formats, ready to be integrated into any other existing software.
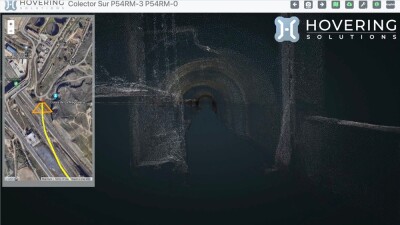
The drones are able to complete large projects in relatively quick amounts of time, as well. Espada tells Geo Week News that a regular drone flight for Hovering Solutions covers more than a kilometer without a battery change or charge in roughly 25 minutes and that they generally scan more than three kilometers in about half of a regular working day, which they consider a separating factor from their competition. He added that their longest flight to date, in which they flew through an underground hydro tunnel, their drone flew seven kilometers autonomously, which they believe is a worldwide record.
Speaking of which, in addition to that Hovering Solutions also provides a report of defects within the mapped infrastructure. Right now, that is not done via AI, but instead with a Hovering Solutions team member with experience in this field flagging potential issues from their look through the images.
It’s this full workflow – manufacturing the drones, flying the drones, providing the raw georeferenced images and 3D model, and a PDF report of detected issues – that Espada believes separates his company from the competition. “The main difference is that we manufacture the whole thing,” he said. “The size of the vehicle, including the payload, is much smaller. This is why we can fly through these risky areas, which are narrow water tunnels. In wastewater tunnels, we could have a lot of factors affecting the navigation, including dense fog, flushable wipes hanging from the ceiling, water coming from different side tunnels, etc. There is a big risk to send one of these small drones through a one-kilometer tunnel with unknown conditions. We are able to do that because we have our own technology.” He added that in more than 150 operations, the company has only lost two drones.
Autonomous inspections
While the end-to-end workflow is a difference-maker among competitors, what generally stands out to potential customers is of course the autonomous flying. In the UAV industry, there isn’t a widely agreed upon system of rating autonomy levels the way there is in the autonomous vehicle space, and Espada doesn’t really think of things in that way. Instead, he says, “Our systems are fully autonomous in linear infrastructure.” That is to say, if they are flying through a tunnel that has extensions off to the side, the drone can’t currently fly into one of these side tunnels. It has to stay in the linear structure. However side tunnels, splits or multipath are detected by the drone in real time, rejecting those paths differing from the target of the inspection.
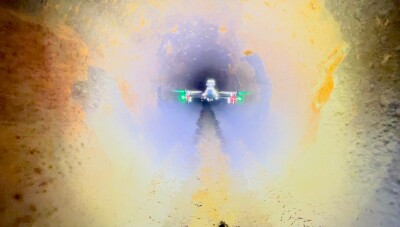
That said, this doesn’t mean that they can only fly through clean, linear spaces. Espada told Geo Week News, “If there is an obstacle, the drone is able to avoid the obstacle and continue the path through the linear infrastructure.” Those obstacles can be a range of things, including pipes coming down through the structure, water coming through different pipes, flushable wipes hanging from ceilings, and plenty of other things. These structures generally aren’t mapped prior to these flights, too, so the pilots aren’t sure what the drone will encounter on its flight until it returns with the data.
Looking Ahead
Hovering Solutions has changed quite a bit since its founding in 2016, starting with just Espada and a single drone. Today, they have 15 employees and a large training and testing facility in Madrid. Espada relays a few changes they are hoping to make in the near future as well, including where they serve customers. Right now, most of their work is in Spain and nearby countries, but Espada tells us they have recently closed their first funding round for international expansion. They have plans to open an entity in the United States and are traveling through and participating in exhibitions in other parts of the world in the Middle East, Asia, and South America as well.
Espada also spoke to potential expansion in terms of use cases and industry sectors which could benefit from these autonomous inspection workflows. Right now, much of the focus is on wastewater and other tunnels, penstocks, and mining, but he looks at nuclear as another area which could benefit.
“They must be sure they don’t put any contaminated part of the building in the wrong container, because this is very, very risky,” Espada said.
Looking forward, though, what Espada is looking to the most is expanding the autonomous capabilities of his drones, as well as shrinking the physical technology. Hovering Solutions integrates their payloads into the drone, which makes expanding capabilities while shrinking the structure a difficult proposition, one into which they are pouring engineering hours.
When asked what developments need to happen to enable these different flight paths to be possible, Espada responded. “More developments, and more engineering hours to allow the drone get a more accurate perception of the surrounding environment. Hardware miniaturization is a big challenge.” He wants to reduce the size of the drone to about 30 centimeters, roughly half the size of their current technology, to be able to fly through pipes of about 0.8 meters, or roughly two-and-a-half feet. This new autonomous drone version is expected to be in operation in the final quarter of this year.
Even with their current technology, though, Espada notes that there is some skepticism among municipalities until they actually see it. “They have to see the technology in action, otherwise they don’t believe that it’s actually just an hour. It sounds futuristic, or like it’s coming from a movie.”